With competition at an all-time high, seamless handling of customer orders from initial placement to delivery is vital to maximizing customer satisfaction and achieving long-term growth in the warehouse fulfillment business.In this complete guide to order fulfillment management, we highlight the most:
- Important processes
- Technologies
- KPIs
- Best practices for warehouse managers focused on optimizing the order fulfillment process
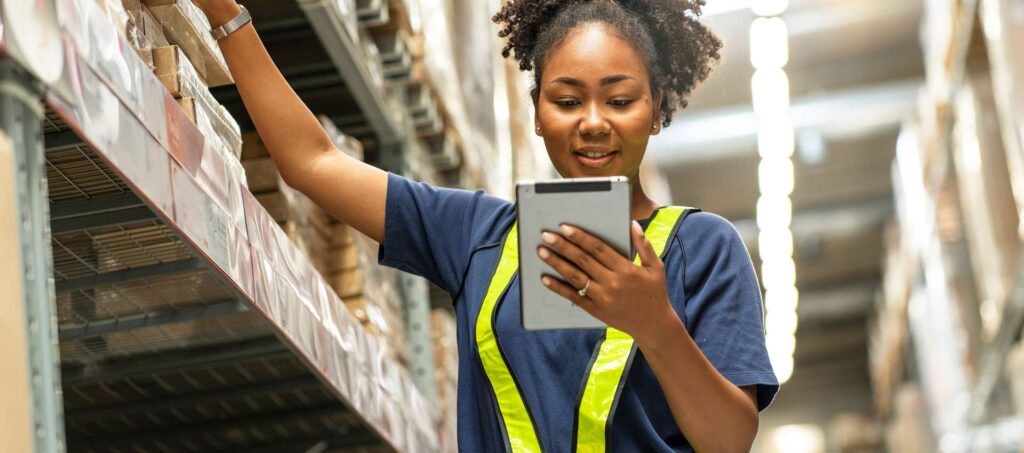
From choosing the right order picking strategy to inventory counts and quality control, you’ll learn exactly what it takes to achieve order fulfillment excellence that will delight your customers and enhance efficiency and profitability in your order fulfillment center.
What is Order Fulfillment?
Order fulfillment is a warehouse function that encompasses the entire process of receiving and validating product orders, picking the inventory for those orders from the warehouse storage area, packaging orders, and shipping orders to the customer.Order fulfillment management involves:
- Controlling and optimizing the order fulfillment process
- Ensure that orders are filled accurately and delivered on time
- Maximize customer satisfaction.”
Order fulfillment management can also include other aspects of warehouse operations management that drive speed and accuracy in the order fulfillment process, such as managing inventory levels in the warehouse, optimizing the warehouse storage layout, and streamlining the reverse logistics process.
Understanding the Order Fulfillment Process
Let’s start with a short look at some of the critical steps involved in the order fulfillment process, beginning with inventory receiving and putaway - the process that brings new stock into the warehouse.
1. Inventory Receiving and Putaway
Warehouse fulfillment centers must have inventory on-hand in order to fulfill customer orders in a timely manner. To maintain adequate inventory levels, warehouse managers must maintain supplier relationships, order new inventory from suppliers as needed, and implement a consistent process for receiving new inventory and putting it away in the warehouse.“Inventory receiving and putaway includes:
- Checking new shipments for damaged or defective goods
- Counting new inventory to verify order completeness
- Sorting new inventory by putaway location
- Transporting new inventory to its storage location in the warehouse”
2. Inventory Management
As new inventory is received and put away in the warehouse storage area, it can also be registered in the fulfillment center’s software inventory management system. Inventory management is the process of tracking inventory and monitoring inventory levels as products move through the fulfillment center. A streamlined approach to inventory management leverages technologies like barcodes and RFID scanning to automate the process. Effective inventory management makes it easier for warehouse operations managers to monitor inventory levels, measure SKU velocity, calculate optimized safety stock levels and reorder points for important SKUs, and maintain adequate inventory to enable the order fulfillment process.
3. Order Processing and Validation
The order fulfillment process is initiated when your fulfillment center receives an order from a customer. Each order must be processed and validated before the fulfillment process can move ahead. Order processing and validation includes steps like:
- Verifying that all correct information has been provided by the customer,
- Verifying that the order meets specific criteria, such as minimum order quantity,
- Verifying that the warehouse has adequate inventory on-hand to fulfill the order,
- Processing the customer’s payment for the order or checking the customer’s credit account to ensure their credit limit is not exceeded, and
- Confirming order validation with the customer.
4. Order Picking and Packing
Once an order has been processed and validated, the next steps are order picking and packaging the order for shipment. Large fulfillment centers use warehouse management system (WMS) software to generate route-optimized picking lists, making it faster and easier for order picking teams to retrieve items from the warehouse for multiple orders.
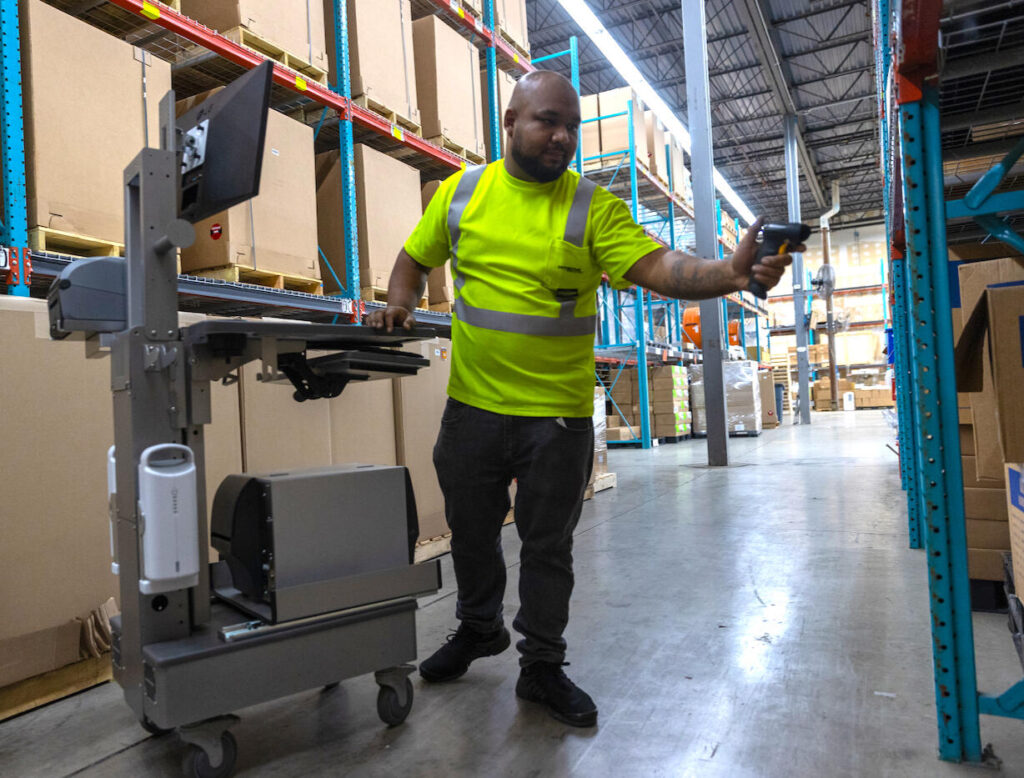
Those items are transported to a packaging area where they are inspected for any damage or defects and packaged with the right materials to preserve their condition in transport to the customer. The last step is applying a shipping label with the customer’s address.
5. Order Shipping and Delivery
Once a customer’s order has been picked and packaged in the warehouse, the final step is to ship that order to the customer.Warehouse operations managers must choose the right shipping partners to maximize customer satisfaction and profitability, accounting for factors like:
- Cost
- Delivery speed and reliability
- Destination
- Type of products being shipped.
Fulfillment centers often apply tracking numbers to outbound packages, allowing customers to track the shipment until it arrives at the destination.
Critical KPIs for Order Fulfillment Management
Tracking the right warehouse success metrics or KPIs can help warehouse managers measure the success of their efforts to optimize order fulfillment management. Below, we recommend three KPIs that should be measured and tracked to assess the order fulfillment performance of a warehouse distribution center.
1. Order Cycle Time
Order Cycle Time is a KPI that measures the average time between when an order was placed and when it was shipped from the fulfillment center. Reducing order cycle times through increased process efficiency helps ensure that customers get their products as quickly as possible after placing an order. Minimizing order cycle time drives customer satisfaction and should be considered a key objective of order fulfillment management.
2. Perfect Order Rate
Perfect Order Rate is a warehouse fulfillment metric that measures how often orders are sent to customers successfully without any negative incidents. To be considered perfect, several criteria must typically be satisfied, the order:
- Arrives to the customer on time,
- Is accurate and complete as per the customer’s order,
- No damage or defects
- Sent with the correct invoice, shipping labels, and documentation.
When any of these conditions is not met, the customer has a negative experience and the warehouse must spend valuable time and money to correct the mistake. A central goal of order fulfillment management is to increase the perfect order rate as close to 100% as possible.
3. Return Rate
Return rate is a KPI that measures the percentage of products returned by customers. A high return rate indicates low levels of customer satisfaction, while a low return rate indicates that your products and order fulfillment processes are meeting customer expectations.
5 Order Fulfillment Management Best Practices You Should Know
1. Leverage Demand Planning
Demand planning is a critical aspect of order fulfillment management that involves using historical sales data, market trends, and customer behavior patterns to forecast demand for specific products. Demand planning helps warehouse managers know how much inventory should be ordered to prevent out-of-stock situations and ensure customer satisfaction.Inventory management and WMS software systems make it easy for fulfillment centers to track historical sales data and use it to project future demand for their products.
2. Maintain Accurate Inventory Counts
Every fulfillment center needs a system for maintaining accurate inventory counts. Knowing precise inventory levels helps warehouse managers ensure the availability of stock to meet customer demands, determine when to reorder stock, prevent theft or shrinkage, and manage costs.For warehouses with automated inventory tracking, manual inventory counts help verify the accuracy of digital counts, identify shrinkage, and identify process gaps that contribute to inaccurate inventory counts.
3. Optimize Your Warehouse Layout
The layout of your warehouse can have a significant impact on the overall efficiency of your order fulfillment process. Optimizing your warehouse layout includes decisions like:
- Designating specific areas for each process (e.g. receiving, storage, packaging, etc.),
- Optimizing your warehouse receiving area layout,
- Building tall shelving to utilize vertical storage space,
- Making storage aisles the appropriate width based on storage needs and equipment usage,
- Storing high-velocity SKUs near the packaging area for fast picking,
- Grouping products strategically to shorten order picking routes and increase efficiency,
- Breaking up long aisles and leaving gaps to enable faster order picking
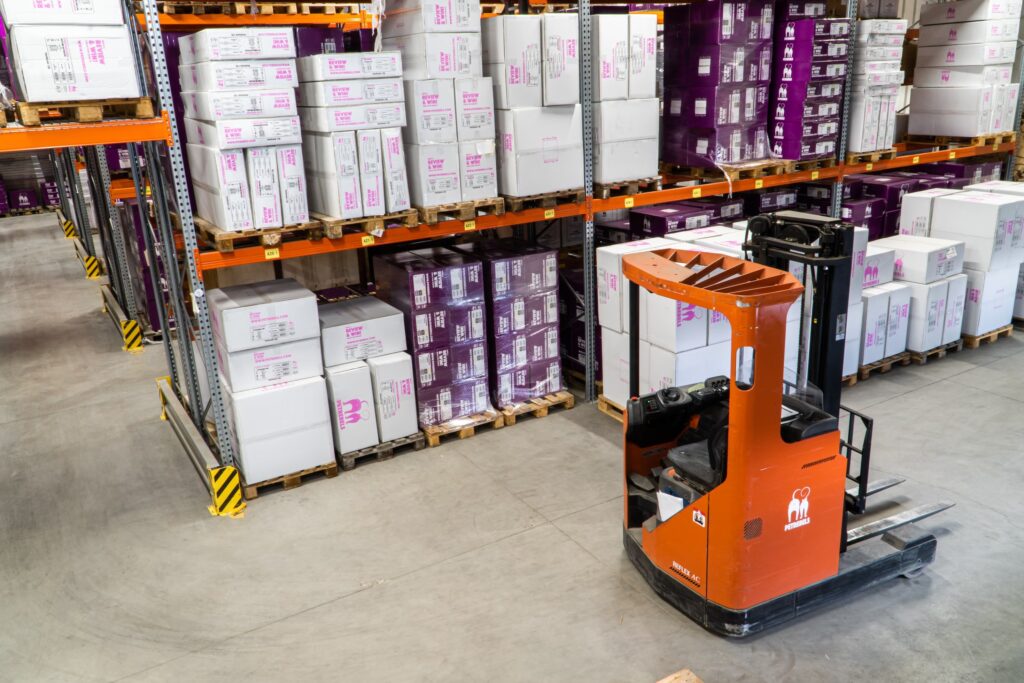
4. Choose the Right Order Picking Strategy
Figuring out the right order picking strategy for your warehouse can help you reduce the cost of warehouse picking and accelerate the order fulfillment process.. Simple strategies like Discrete Picking (where each order picking is assigned one order at a time) work well in low-volume warehouses. But there are more efficient strategies for larger warehouses, including:
- Zone Picking, where each order picker only picks items from a specific zone of the warehouse,
- Batch Picking, where order pickers work on retrieving items for multiple orders at the same time, or
- Cluster Picking, where order pickers are assigned to pick clusters of items that are stored close together.
The best warehouse order picking strategy depends on the unique circumstances of your fulfillment center, including the size of your facility, order volume, staffing and equipment, and the specific products you sell.
5. Implement Quality Control Measures
Quality control involves inspecting the work of warehouse operations teams to ensure that orders are being fulfilled correctly. Quality control helps fulfillment centers detect and remedy problematic orders before they are shipped, as well as identify process deficiencies that negatively impact customer satisfaction.Warehouse managers can implement quality control at several different points in the order fulfillment process. Quality personnel can play a role in verifying the quality and quantity of newly received inventory, checking the accuracy of picked orders, and ensuring that parcels are packed and labeled correctly for shipping.Read: 39 Tips for Running a Successful Warehouse
Technology Powers Exceptional Order Fulfillment Management
Warehouses are moving away from paper-based order management systems and leveraging modern technologies to streamline and automate the order fulfillment process. Software tools like OMS and WMS help streamline and automate order fulfillment workflows, while inventory management software integrates with data capture technology to automate inventory tracking. Fulfillment centers need computer workstations and additional hardware peripherals to operate these technologies. There’s also materials handling equipment and even warehouse robots that help move inventory around the fulfillment center.Below, we highlight the role these technologies play in order fulfillment management.
1. Inventory Management Systems
Inventory management systems are software products that help warehouse operations managers track and monitor inventory as it moves through the fulfillment center. Inventory management software helps warehouse managers track and store information about inventory levels in the warehouse, along with important details about products, pricing, and suppliers. Modern inventory management systems deliver features that help warehouse managers automate the process of inventory tracking. This can include things like barcode and RFID integration, as well as integration with OMS and payment processing systems to automatically update stock availability as products are ordered by customers.
2. Order Management Systems
An order management system (OMS) is a software system that makes it faster and easier to manage the order lifecycle, from order receipt and entry to processing, validation, and fulfillment. OMS software allows warehouse managers to efficiently track orders and provide status updates to customers throughout the order fulfillment process. OMS systems can also leverage integrations with payment processing systems and customer relationship management (CRM) tools, helping to streamline customer communication and track both payments and refunds.
3. Warehouse Management Systems
A warehouse management system (WMS) is a software application designed to help streamline and automate warehouse operations and order fulfillment processes. Modern WMS solutions combine the features and functionality of inventory management and OMS with additional capabilities like:
- Warehouse receiving process management and inspection reports,
- Warehouse slotting systems and layout optimization,
- Picking optimization, including the ability to generate pick lists based on different picking strategies,
- Labor management and scheduling,
- Supplier and shipping carrier relationship management,
- Returns/reverse logistics management, and
- Integration with ERP, accounting, and other financial systems.
4. Automatic Identification and Data Capture Systems
Automatic Identification and Data Capture (AIDC) technologies include both barcode and RFID scanning systems that help automate the process of tracking inventory in the warehouse.Barcodes can be applied to individual products, shelves, or bins in the warehouse. Warehouse operations teams equipped with barcode scanners can scan barcodes to update inventory levels, track product movement, and reduce order picking errors.RFID tags can be attached to individual products in the warehouse. These tags send out radio signals that can be picked up by RFID readers and used to update inventory levels or monitor inventory as it moves around the warehouse. RFID technology automates inventory tracking in real time, making it ideal for warehouses with high volume throughput or ones that use high-speed conveyor systems to move inventory.
5. Materials Handling Equipment
Every distribution center needs the right material handling equipment to efficiently move and process inventory in the warehouse. This can include forklifts and pallet jacks, conveyor systems, cranes and hoists, dock lifts, and packaging equipment like stretch wrappers, carton sealers, and strapping machines.
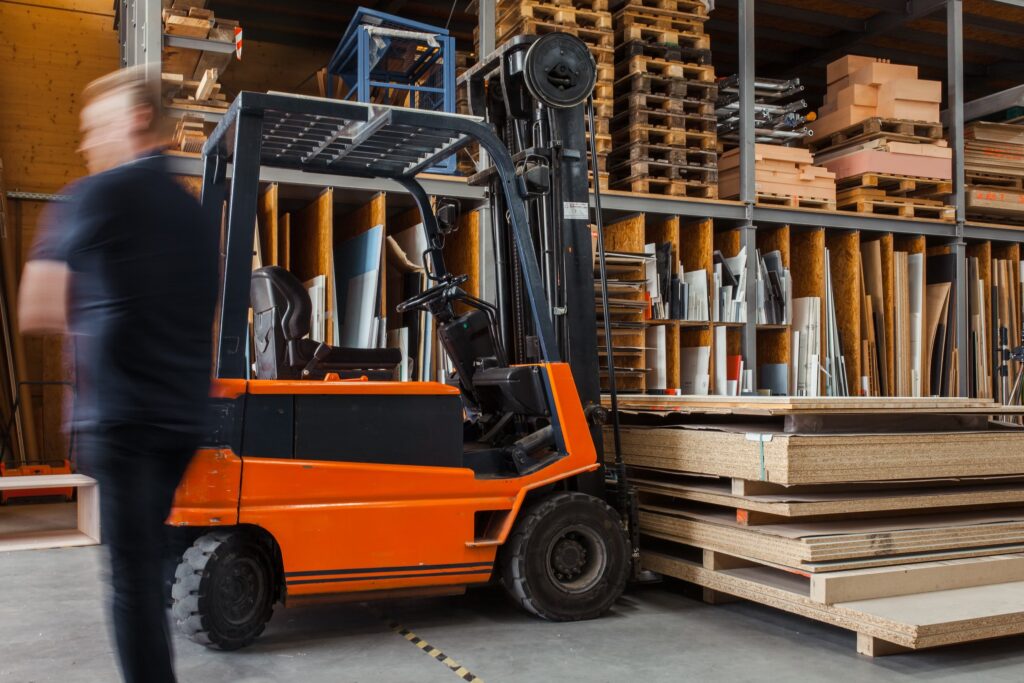
Material Handling equipment can be used in every stage of order fulfillment management, from inventory receiving and putaway, to picking, packaging, and shipping.
6. Powered Mobile Workstations
Warehouse fulfillment centers that depend on inventory management or WMS software for daily operations need computer workstations that can be readily accessed by warehouse operations staff. Positioning fixed workstations in key areas of the warehouse (e.g. receiving, putaway area, order picking area, etc.) is one potential solution, but this leads to inefficiency and wasted steps as employees must travel to (and from) the workstation anytime they need to use WMS or other software programs.Mobile computer carts can be powered by rechargeable battery systems and configured with computer systems, RFID readers, or barcode technology as needed. Mobile workstations allow warehouse operations staff to mobilize technology in the warehouse, increasing the efficiency of inventory counts, putaway, and order picking processes.
7. Robotics and Automation Technologies
The most modern warehouses are already leveraging robotics and automation technologies to support the process of order fulfillment management. Autonomous Mobile Robots (AMRs) use specialized sensors to navigate the warehouse without a human driver. They can be programmed to transport inventory from the receiving area to its storage location in the warehouse, and eventually to the packaging area as part of the order fulfillment process.There are also robots that can auto-pick orders, robots that automate packaging, and robots that help warehouse operations staff lift heavy packages.
Accelerate Order Fulfillment Processes with the DTG Problem Solver Warehouse Cart
The Problem Solver Mobile Computer Workstation is a durable, ergonomic, battery-powered mobile workstation, designed and manufactured by DTG to support order fulfillment activities in the warehouse.
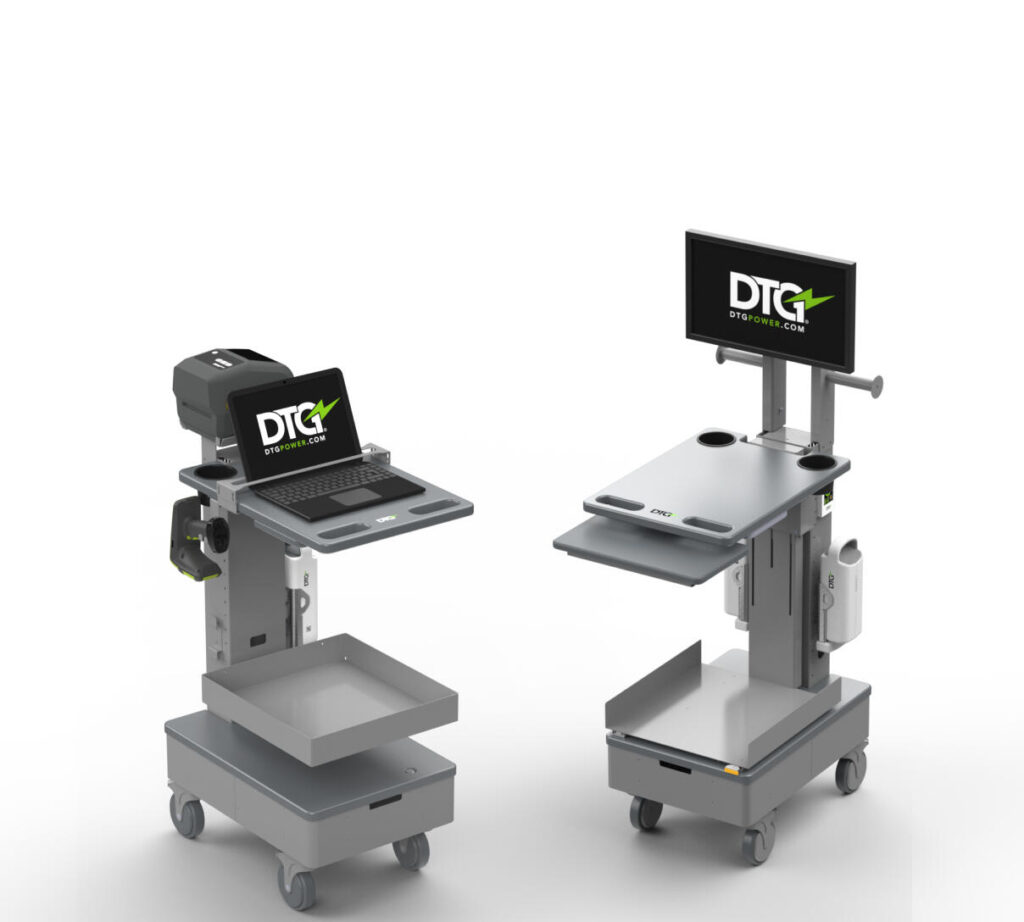
Deploy our Problem Solver carts in your warehouse to eliminate wasted steps in every aspect of the order fulfillment process - from receiving and storing new inventory, to cycle counting, stock audits, and order picking.
Ready to learn more?
Contact us for a free virtual demo and discover how the busiest fulfillment centers are maximizing efficiency with DTG Problem Solver warehouse carts.